Welding is a fabrication or sculptural process that joins materials, usually metals or thermoplastics, by using high heat to melt the parts together and allowing them to cool causing fusion. Welding is distinct from lower temperature metal-joining techniques such as brazing and soldering, which do not melt the base metal.
WPQ: Welder Performance Qualification
WPQ/S: Weld Procedure Qualification/Specification
WPS: Welding Procedure Specification is the formal written document describing welding procedures, which provides direction to the welder or welding operators for making sound and quality production welds as per the code requirements
PQR or WPQR: Qualification Record. A PQR is a record of a test weld performed and tested (more rigorously) to ensure that the procedure will produce a good weld. Individual welders are certified with a qualification test documented in a Welder Qualification Test Record (WQTR)
WQTR: Welder Qualification Test Record that shows they have the understanding and demonstrated ability to work within the specified WPS
LISL: Line Inspection Summary List
ITP: Inspection and Test Plan
An Inspection and Test Plan (ITP) or test plan is a document detailing a systematic approach to testing a system or product (e.g. material, component, machine, package, software, etc.) such as a visual inspection, dimension inspection, welding inspection, function test, factory acceptance test, etc. and participation of all parties
MIG – ‘MIG’ stands for ‘Metal Inert Gas’ welding, but you might also see it referred to as ‘GMAW’ (‘Gas Metal Arc Welding’), or ‘MAG’ (‘Metal Active Gas’ welding). This is one of the most common welding techniques – and one of the easiest to learn – so it’s great for both beginners and large scale production.
MIG uses a consumable electrode and an argon-carbon dioxide shielding gas to create strong welds on both thin and thick sheets of metal.
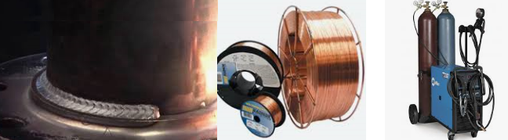
TIG – ‘TIG’ stands for ‘Tungsten Inert Gas’ welding, which is the same as ‘GTAW’ (‘Gas Tungsten Arc Welding’). On paper TIG seems quite similar to MIG, except that the electrode is non-consumable and the shielding gas typically has an argon-helium composition.
TIG is a more difficult process to master than MIG as it needs a more precise technique. As a result, it’s usually used by more experienced welders or for delicate projects which need a clean finish.
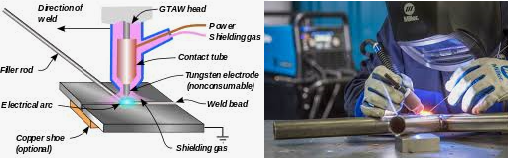
FCAW – ‘FCAW’ stands for ‘Flux-Cored Arc Welding’. This process uses different equipment to MIG and TIG welding, because although the electrode is a continuously-fed consumable one (like with MIG), it has a flux at its core. This flux eliminates the need for a separate shielding gas, which means that it’s suitable for outdoor projects and windy conditions.
FCAW can produce dangerous gases, so it’s essential to wear adequate protection such as a welding helmet. However, if proper care is taken with safety as well as technique, then FCAW is a brilliantly fast, portable process which is ideal for manufacturing.
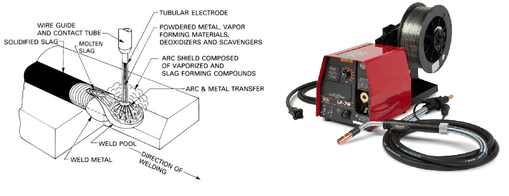
SMAW – ‘SMAW’ stands for ‘Shielded Metal Arc Welding’, but you might commonly hear it being referred to as ‘stick welding’. Like FCAW, SMAW uses flux to protect the weld pool from damaging atmospheric gases – the only difference is that in SMAW the flux coats the electrode, whereas with FCAW it’s at the center.
SMAW is a slightly easier process to learn than FCAW as it requires less equipment and a less refined technique. It can be used with most metals – including thick, industrial steel and iron – making it one of the most popular and widely used welding techniques ever.
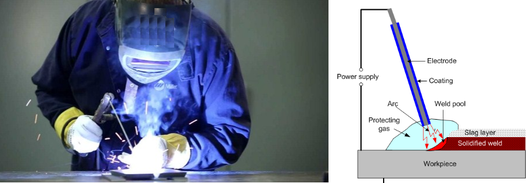
GMAW – ‘GMAW’ stands for ‘Gas Metal Arc Welding’, which is a term that encompasses both MIG and MAG welding. All three of these processes use the same method of forming an electric arc between an electrode and the metal. This heats the metal and causes it to melt, creating a joint which fuses the metal pieces together.
GMAW needs a shielding gas to protect the weld pool from atmospheric gases, so it isn’t suited to outdoor projects. This is because if any wind blows the gas away from the weld pool, you will end up with defective, porous joints. However, when used indoors GMAW is an incredibly versatile process.
There is a long list of other abbreviations which you might come across during your welding career. Here is a small selection of some of the most common
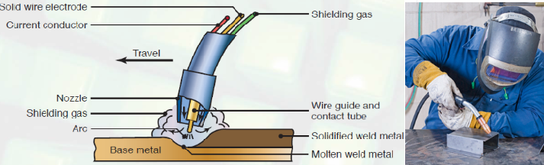
Orbital welding is a specialized area of welding whereby the arc is rotated mechanically through 360° (180 degrees in double up welding) around a static workpiece, an object such as a pipe, in a continuous process.. In orbital welding, computer-controlled process runs with little intervention from the operator.The process is used specifically for high quality repeatable welding.
The process was developed to addresses the issue of operator error in gas tungsten arc welding processes (GTAW=TIG)
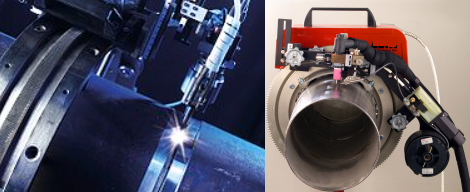